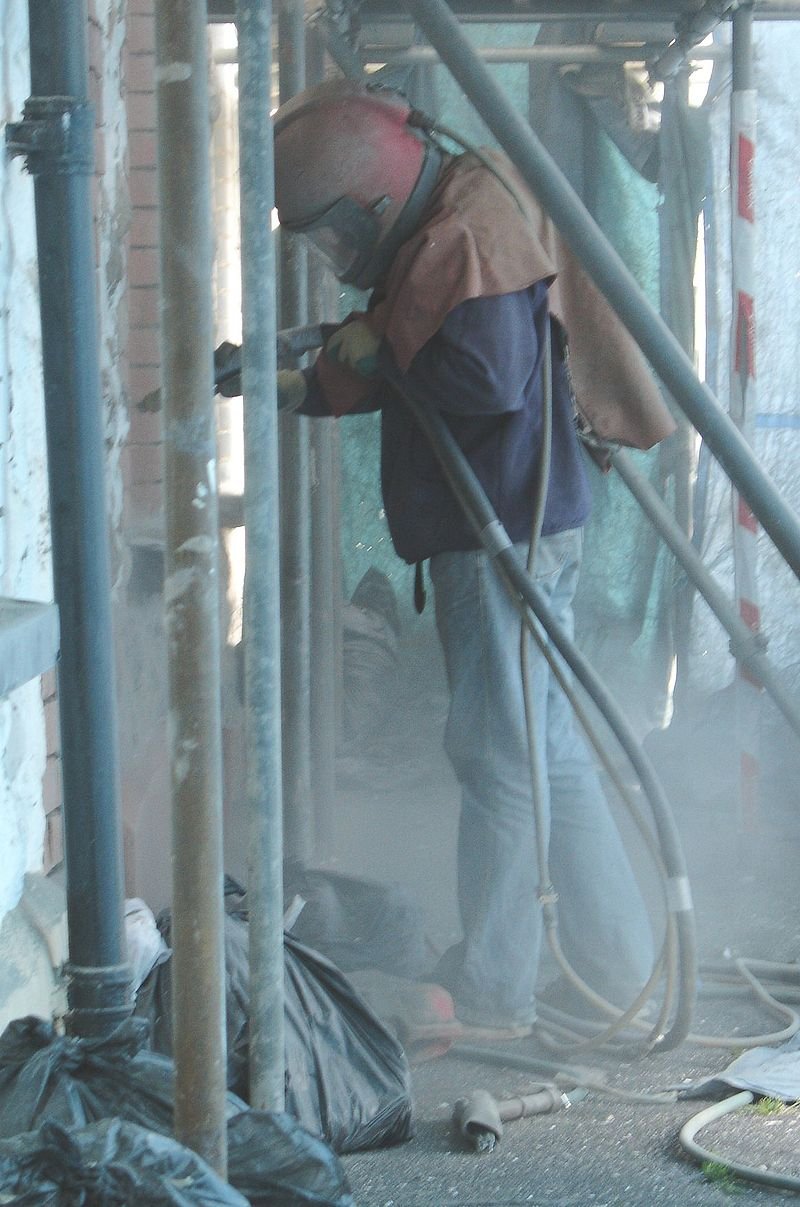
Vapor honing is a new application of surface roughing or buffing technology. It takes the concept of a high-speed abrasive jet that's used in many abrasive blasting processes and reduces the pressure exerted on the material by using a fine mist of compressed air. Because of this reduced pressure, it allows for much greater fluid flow rates and allows for much faster grinding speeds with less effort. The result is a much smoother and quicker finishing time than is possible using traditional methods.
There are many industries that have seen tremendous benefit using vapor blasting technologies. One of these industries is the metal fabrication industry. Using vapor blasting equipment has helped to lower the cost and energy consumption associated with metal fabrication. Many metals can be used for fabrication, such as aluminum, stainless steel, and nickel titanium. Some of the metals that can only be fabricated using a high-speed air abrasive jet device are titanium and copper. With the advancements in vapor blasting equipment, metal fabrication has been revolutionized, and new designs can be produced more quickly and economically than ever before.
In the case of parts washing and polishing, another sector that has greatly benefited from the use of this technology is the automotive industry. Parts washing and polishing involve the removal of heavily stained and oxidized parts. In fact, auto body shops use some form of abrasive spray on their freshly polished parts and other parts. This prevents the vehicle from attracting rust, which in turn prevents rust buildup, which in turn means that the vehicle will retain a higher resale value over time. There are a wide variety of industries that can take advantage of vapor blasting for parts washing, but one of the fastest growing uses is the auto parts market.
When an abrasive blasting operation is first starting up, it's important to carefully select the kind of abrasive being used. Today, two of the most popular choices are titanium and copper. However, in the past, the most commonly used mediums were steel and aluminum. These materials all have their own unique properties, and so the manufacturer would decide which to use based upon both their cost and speed of use. Other factors to consider when making your selection include how long the parts washing and polishing will take to complete, as well as if the machine will need frequent recharging or will need to be continually cooled down after each use. A final consideration that should be part of your decision-making process is whether to purchase a machine that runs off of a battery or if you plan to have the unit constantly available for use.
A final advantage of vapor blasting equipment is that it can sometimes replace traditional sandblasting or abrasive jetting. Although these methods have been around for decades, they are rarely used today due to the lack of positive results. On the other hand, vapor blasting provides much better control and efficiency and may soon prove to be the industry standard. As time goes on, this new method of finishing can only benefit the manufacturers and fabricators who are looking to improve the quality and overall value of their work.
There are many different industries that have made use of vaporizing systems in the past and are now experiencing increased success with their products. For example, fabricators often times turn to abrasive sandblasting when they run into problems with chipping or bonding. However, these two processes take too much time and effort and are not cost effective for most companies. Abrasive jetting is also very expensive and requires too much maintenance. If these problems are not solved by using vaporizing systems, these companies will often have to spend additional money on new equipment. Vapor honing machine offer many advantages and are quickly becoming the industry standard in many places. For more enlightenment about vapor honing, see site: https://www.encyclopedia.com/science/encyclopedias-almanacs-transcripts-and-maps/abrasives.